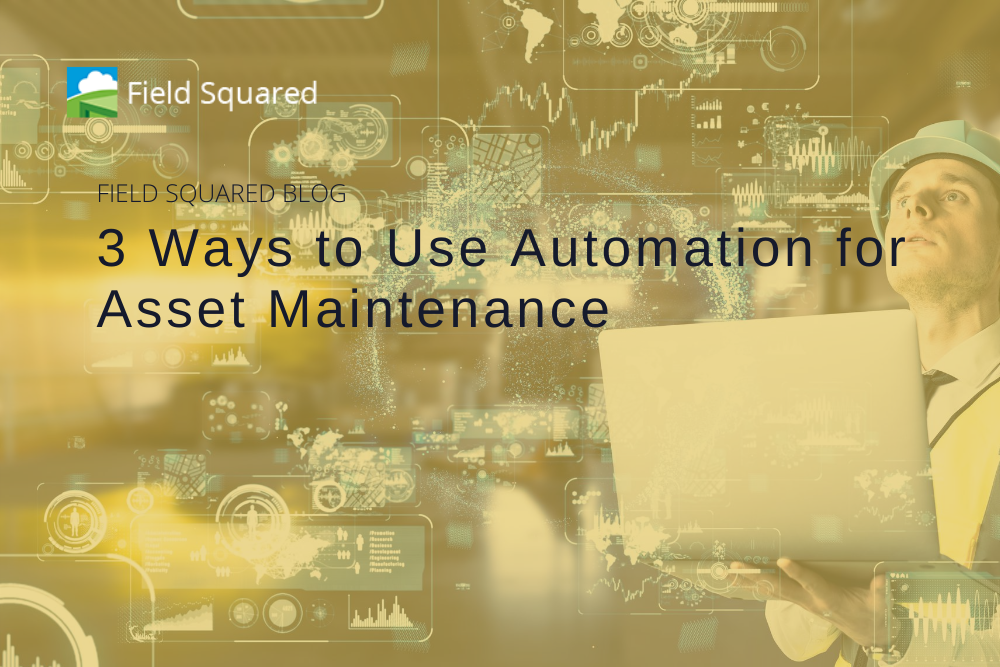
For many asset-intensive industries, such as manufacturing and utilities, managing, servicing and maintaining internal- or customer-owned assets is a massive undertaking. Effectively conducting field operations work without the right information at the right time, hinders productivity at the least and can lead to significant capital spending on downtime/outage events at worst.
Today’s technologies span many possibilities to aid field technicians, while keeping the overarching business operational goals on track. Impactful technology includes IoT, IIoT, wearables, automation software and artificial intelligence tools.
The promise of leading-edge technology sounds miraculous, but many organizations are just beginning their digital evolution. Transformation may be months or years away before being put into practice. And with everyone wanting to move a mile a minute, the reality is it’s not that simple.
Take a step back to identify the true asset maintenance challenges that hinder the daily lives of your field technicians before jumping in. That’s really what I wanted to talk about in this blog.
Over the years, I have talked with many customers about their asset maintenance challenges, designing solutions to solve even the most complex problem.
What I found were common challenges that are readily solvable by applying automation software to do the heavy lifting. That’s how I came up with the following list of three ways to use field service automation software for asset maintenance.
#1: Mitigate Risk: Automate Preventative Asset Maintenance Schedules
The job is never done when it comes to managing, servicing and maintaining assets. For one, machine parts fail, buildings age, and equipment breaks down. That is the nature of the situation.
Controlling the uncontrollable is more about mitigating risk.
For instance, I often see significant lost productivity when a technician is dispatched to a job without the right parts or equipment to complete the work. The lack of inventory management solutions, including mobile inventory transfer tools for technicians, can greatly impact key operating metrics that include:
- First time fix rate
- Number of jobs completed in a day
- Percent complete on a single job
One way to address risk, is through the use of automation for scheduling asset maintenance activities.
The simple act of scheduling recurring service work has the potential to positively impact more than one aspect of an organization’s business operations over and above those already mentioned.
#2: Reduce Data Inaccuracies: Automate Updates Across Multiple Systems
It is common for asset maintenance work to require interacting with more than one system, tool or software. Utility service providers often leverage a GIS provider such as Esri to enrich asset data with other meaningful information.
There may also be a need for a knowledgebase of decision-making support workbooks, step-by-step guides, user manuals and other documentation that resides in a different system.
Whatever the case may be, it is evident re-entering asset maintenance data is a common practice.
Inaccurate data is a product of combining manual processes with multiple systems of record. Having one system of record—a single source of truth—should be the ultimate goal for any business that conducts asset maintenance service work. Synchronizing multiple asset registries using Field Squared as the hub, is one such solution.
As an example, a technician responds to an asset maintenance service request. He/She is unable to diagnose the issue and need to reference documentation to walk-through troubleshooting scenarios. A solution is found, and the maintenance work commences. After the work is done, it’s time to schedule a check-in in a few days. The paper form must also be submitted to various internal teams to further document the details.
I realize this is a simple scenario on the surface, but the innerworkings are where the problems arise. Let’s break it down by problem and how automation can be applied.
Problem 1: A paper form was used which has inherent deficiencies, such as legibility and logistics to submit completed forms.
Where Automation Can Be Applied: Digital mobile forms are the perfect place to apply automation for asset maintenance activities. Digital forms eliminate legibility issues and completed forms can be automatically sent to anyone—customers, partners, operations, management. More complex workflows can also be applied to automate notifications based on individual form fields. But that is a topic for another blog post.
Problem 2: Decision-making support documentation was needed, which most likely meant going into another system or trying to pull up a website to view the material. If connectivity was an issue, this could add to the time on the job.
Where Automation Can Be Applied: An easy to use, yet comprehensive field service mobile application, should have the capability to consolidate everything directly within the work order itself. The technician should not have to switch systems, pull up a website or worry about connectivity.
Problem 3: How was the future maintenance check-in documented and scheduled? Chances are an email (or even a text message) was sent by the technician to operations to schedule it.
Where Automation Can Be Applied: A simple check box on the mobile form would be enough that, once submitted, a notice is automatically sent to the operations team. Done.
#3: Communicate: Automate Status Updates and Notifications
In a perfect world all asset maintenance work would start and be completed on-time like clockwork. Reality has different ideas.
No matter how much planning goes into documenting how long a certain type of asset maintenance task will take, there may be times when the technician is delayed getting to the next scheduled service task.
By applying automation across job status updates, operations managers, customers, or partners are kept apprised of changes to the schedule. In effect, it allows others to better plan their day and provides the technician peace of mind that someone is not actively waiting for them. A little communication goes a long way.
Another way to leverage automation in work order management, is through email. When a ticket or service request comes in from an email, a work order is automatically created and assigned to a technician or to the team that handles the asset maintenance.
Oftentimes, SLAs and time to respond constraints are in place when an asset maintenance request comes in. A rapid response is critical where any delay can wreak havoc for a business. Cases like this are a prime example where automation eliminates the burden of remembering what’s what. Here, the use of escalation rules via automated workflows are easily applied, such as the following example:
- If technician does not acknowledge asset maintenance request in 15 minutes, send second notification
- If technician does not acknowledge second asset maintenance request in another 15 minutes, send a third notification to the technician
- AND Send a new notification to the technician’s supervisor
The escalation continues up the chain until someone has taken ownership of the ticket and the work is complete.
On their own, these three simple ways to use field service automation software for asset maintenance work moves the needle, but together, they may just change your world.

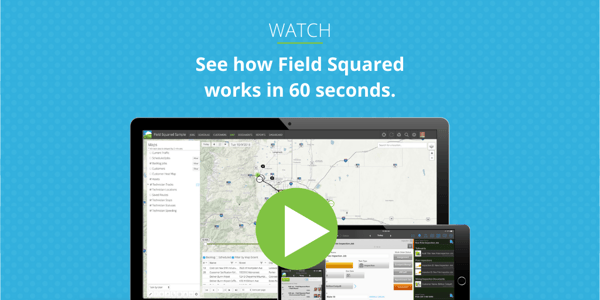