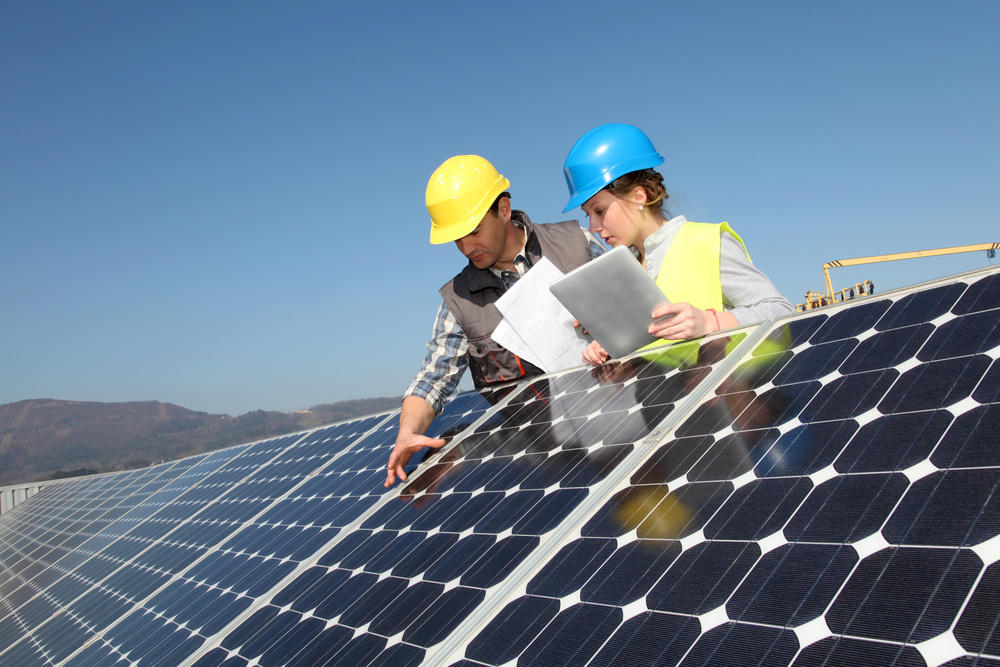
That’s why field service inventory management is more than just tracking parts in a warehouse. It’s a strategic enabler that keeps operations running smoothly, supports technician productivity, and improves the overall customer experience.
In this article, we’ll explore the growing importance of inventory management in field service operations and break down the steps leading organizations are taking to get it right.
Inventory Visibility: The First Step to Operational Efficiency
For many field service companies, visibility is the biggest hurdle in managing inventory. Without a centralized system, it’s hard to know what’s available, where it is, or how soon it can be restocked.
Relying on spreadsheets or disconnected systems leads to problems like:
- Unnecessary reorders
- Lost or misplaced parts
- Overstocked or understocked inventory
- Time-consuming manual tracking
Modern field inventory management solutions offer a real-time view across all storage points—from warehouses and service vans to temporary job site stock. When everyone from dispatchers to technicians can see what’s in stock, you eliminate guesswork and prevent costly delays.
Enabling Field Technicians with the Right Tools
Technicians are the ones using the parts, so why are they often left out of the inventory management conversation?
Leading companies are flipping that model. They’re using mobile-first tools that let field teams:
- Check inventory levels before heading to a job
- Record part usage instantly
- Flag items for restock directly from the field
This approach not only empowers technicians, it creates cleaner, more accurate inventory records. And it ensures the system reflects what’s actually happening in real time—something that manual end-of-day logs can never match.
Automating Inventory Tasks for Scalability
The more your operations scale, the harder it becomes to manually manage inventory. At some point, even the most diligent back-office staff can’t keep up with technician needs, vendor deliveries, and maintenance part usage.
That’s where automation pays off.
Automated field service inventory management tools can:
- Trigger restock orders based on low thresholds
- Auto-generate part kits for standard job types
- Flag unusual usage trends that may indicate loss or theft
- Integrate returns and warranty tracking
By building automation into your workflows, you streamline repetitive tasks, reduce human error, and keep parts moving without bottlenecks. Teams that pair automation with strong route optimization tools also reduce unnecessary travel and get more done each day.
Standardizing Parts to Simplify Operations
Standardization isn’t about limiting technician flexibility—it’s about removing chaos from the system.
By standardizing the parts used across similar jobs or regions, you can:
- Predict usage more accurately
- Simplify training for new hires
- Reduce procurement complexity
- Minimize stock variety, making inventory easier to manage
It also helps reduce the risk of a technician showing up with the wrong part or having to call in for clarification. Simpler parts lists mean faster, more confident job completion—and more consistent service delivery.
This can be especially helpful when addressing persistent field service challenges like scheduling conflicts, job delays, or part shortages.
Connecting Inventory with Scheduling, Billing, and Procurement
Inventory doesn’t operate in a vacuum. It connects directly to other key systems in field service management, especially scheduling and procurement.
When your inventory system integrates with your scheduling tools, you can:
- Confirm part availability before a job is assigned
- Avoid last-minute reschedules due to out-of-stock items
- Better align technician schedules with part delivery dates
Likewise, integrating inventory with billing ensures that every part used on a job is properly accounted for and invoiced. This improves your margins and reduces disputes over charges.
A connected system turns field inventory management into a core part of your operational success, rather than a support function buried in the background.
Real-Time Data for Proactive Decisions
Accurate data is the foundation of strong decision-making. And when it comes to inventory, real-time data helps you stay proactive rather than reactive.
For example, with up-to-date inventory insights, you can:
- Forecast demand based on seasonal trends
- Identify slow-moving parts and avoid overstocking
- Track usage by technician or job type
- Spot inefficiencies in your supply chain
Some teams even tie inventory performance to field workforce location tracking, allowing them to match part availability with technician proximity—ensuring jobs are handled as efficiently as possible.
Better Inventory, Better Customer Experience
At the heart of all of this is the customer. When a job is delayed or rescheduled because a part isn’t available, customers notice. And when jobs are completed in one visit, with no surprises or wait times, they remember that too.
Good field service inventory management leads to:
- Higher first-time fix rates
- Reduced technician downtime
- Fewer scheduling disruptions
- More reliable service outcomes
It’s a win for everyone—your technicians, your back office, and your customers.
And when your team is running more efficiently, optimizing field service routes and keeping inventory stocked in the right locations, you build a foundation for scalable growth.
Conclusion: Inventory Management as a Strategic Advantage
The importance of inventory management in field service has never been clearer. It’s not just a logistics task—it’s a strategic function that impacts cost control, service quality, employee productivity, and customer satisfaction.
By investing in better visibility, empowering your field teams, and automating what you can, you’ll position your company to move faster, reduce waste, and deliver better service—all without overcomplicating your operations.
Field service may be complex, but your inventory system doesn’t have to be.