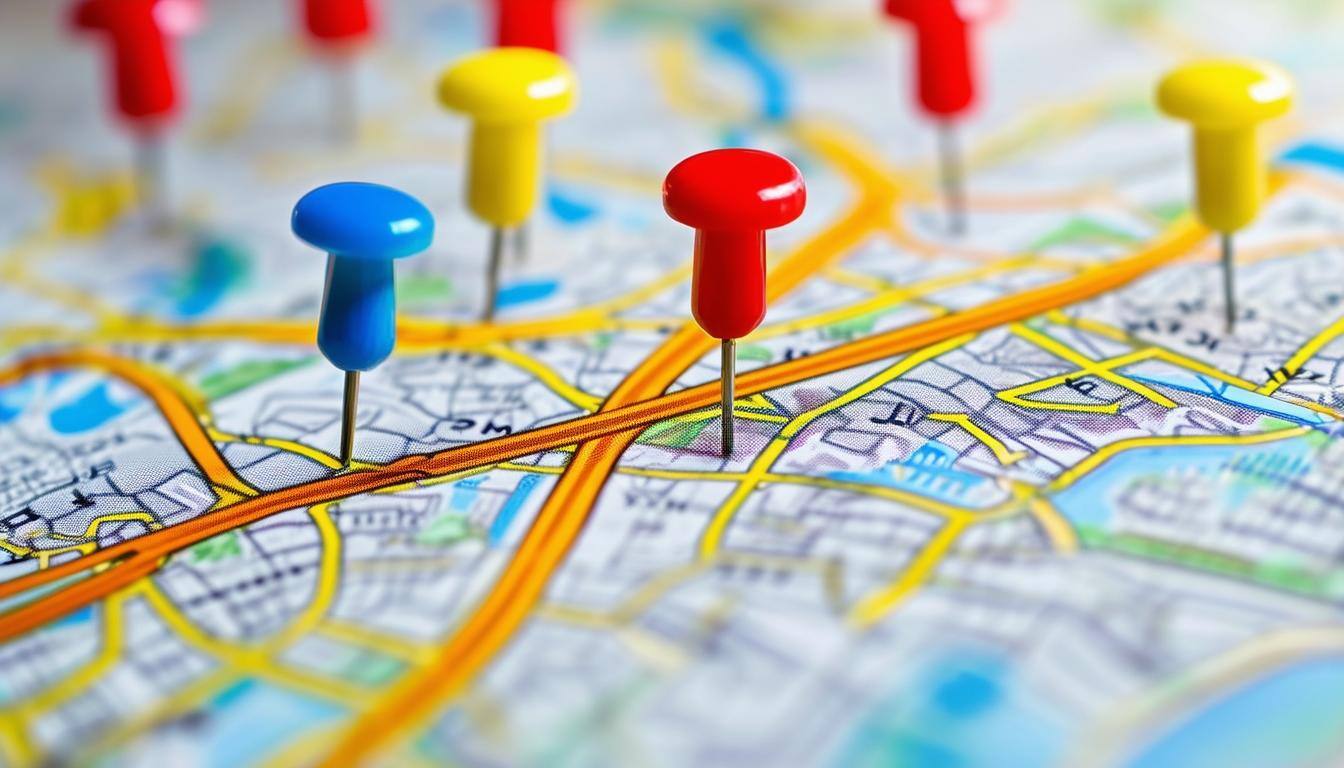
I’ve spent years working in field service management, and if there’s one thing I’ve learned, it’s that field service scheduling is the backbone of any efficient operation. Getting the right technician to the right job at the right time can make or break your business. Yet, I’m still surprised by how many companies rely on outdated manual scheduling methods, leading to inefficiencies and frustration.
If you’ve ever had to reschedule a job last minute, scramble to find an available technician, or deal with customer complaints about delays, you know exactly what I’m talking about. That’s why I’m passionate about helping businesses optimize their scheduling processes with the right technology.
In this blog I’ll walk you through what is service scheduling, why it’s so important, and the best practices I’ve found to improve your scheduling for field service operations.
What is Field Service Scheduling?
At its core, field service scheduling is about planning, assigning, and managing service jobs for field technicians. It’s more than just booking an appointment—it’s making sure work orders are properly assigned, dispatching the right personnel, and ensuring jobs are completed efficiently.
When I first started in this industry, I quickly realized that field service planning goes beyond just filling a technician’s schedule. It requires considering factors like:
-
Technician skill level and certifications
-
Proximity to the job site
-
Equipment and parts availability
-
Customer preferences and service history
-
Real-time traffic and route optimization
Without a structured field service scheduling process, businesses run the risk of delays, miscommunication, and unhappy customers. Trust me, I’ve seen it firsthand.
Why is Field Service Scheduling Important?
Over the years, I’ve worked with countless businesses, and the one thing they all want is a more efficient operation. Here’s why scheduling for field service matters so much:
1. Boosts Workforce Efficiency
When schedules are optimized, technicians spend less time driving between jobs and more time actually completing work. Automated field service scheduling tools ensure that each task is assigned to the most qualified technician, reducing unnecessary delays and repeat visits.
2. Improves Customer Satisfaction
Nothing frustrates customers more than waiting for a technician who shows up late—or worse, doesn’t show up at all. With real-time field service planning updates and accurate ETAs, you can provide a seamless customer experience, which keeps them coming back.
3. Reduces Operational Costs
I’ve seen businesses waste thousands of dollars due to poor scheduling for field service. Wasted fuel, overtime costs, and inefficient job assignments all add up. Optimizing routes and technician assignments can significantly cut costs while maintaining high service quality.
4. Minimizes Human Error
Manual field service scheduling is prone to errors—double bookings, missed appointments, inefficient job assignments. I’ve worked with teams that struggled with this, but once they switched to automated field service scheduling software, the mistakes virtually disappeared.
5. Scales with Your Business
As companies grow, manual field service planning becomes a nightmare. You can’t keep up with demand if you’re still juggling schedules by hand. That’s where automated scheduling tools come in, allowing you to scale without adding extra administrative headaches.
Must-Have Features in Field Service Scheduling Software
To make field service scheduling truly effective, businesses need the right tools. Here are the must-have features to look for in a field service management solution:
Feature | Description |
Automated Scheduling | Uses AI to assign jobs based on technician availability, skills, and proximity. |
Real-Time Tracking | Provides live field workforce location tracking for better dispatching. |
Route Optimization | Calculates the most efficient routes to reduce travel time and fuel costs. |
Skill-Based Assignment | Ensures the right technician is assigned to the right job based on expertise. |
Customer Notifications | Sends automated alerts about appointment status and estimated arrival times. |
Mobile Accessibility | Allows technicians to access job details, update statuses, and complete reports from the field. |
Integration with Inventory | Ensures technicians have the necessary parts and equipment before arriving at the job site. Learn more about inventory management. |
Work Order Management | Centralizes job tracking, documentation, and scheduling in one system. |
Analytics and Reporting | Tracks key metrics to improve scheduling efficiency and business performance. |
The Power of Route Optimization
One of the best-known examples of route optimization in action is UPS. The company drastically reduced drive time and slashed fuel costs simply by minimizing the number of left turns their drivers took. By using advanced route optimization, they saved millions of gallons of fuel and improved delivery efficiency.
I’ve seen similar benefits in field service management. At Field Squared, we analyzed how route optimization could impact a property management company still relying on manual scheduling. The result? A 6-day workweek was reduced to a 5-day workweek, simply by applying route optimization. That’s a massive productivity boost from a simple process improvement.
If you implement just one change in your field service scheduling process, make it route optimization.
Best Practices for Effective Field Service Scheduling
Over the years, I’ve developed a set of best practices that can help any business improve their field service scheduling process.
1. Use a Centralized Scheduling System
I can’t stress this enough—having a single place where you can see all field service scheduling activities in real-time is a game-changer. Dispatchers can easily manage work orders, track technician availability, and respond to last-minute changes.
2. Assign Jobs Based on Skills
I’ve seen too many companies send the wrong technician to a job, only to waste time and money. Assigning jobs based on skill tags ensures the right person is handling each task, which improves first-time fix rates and customer satisfaction.
3. Optimize Routes to Reduce Travel Time
Field service planning should always include route optimization. Reducing unnecessary travel time means technicians can fit in more jobs per day, cutting down on fuel costs and increasing efficiency.
4. Keep Communication in Real-Time
Unexpected job cancellations and emergency requests happen all the time. That’s why real-time communication between field technicians and dispatchers is crucial for maintaining an efficient schedule.
5. Use an Interactive Map for Visibility
Tracking technicians’ locations in real time helps dispatchers make smarter decisions. If an urgent job comes in, they can quickly see who’s closest and available to take it.
6. Automate Notifications and Customer Updates
Keeping customers informed about their service appointments is key to a great experience. Automated notifications can provide estimated arrival times, reminders, and status updates without adding extra work for your team.
7. Ensure Inventory is Managed Efficiently
One of the biggest frustrations I’ve seen in field service is when technicians arrive at a job site without the right parts. Integrating field service scheduling with inventory management prevents this issue and keeps everything running smoothly.
8. Continuously Monitor and Improve
I always recommend tracking key metrics like response time, job completion rates, and customer feedback. This helps businesses continuously refine their scheduling for field service strategies over time.
Final Thoughts
When it comes down to it, field service scheduling isn’t just about making appointments—it’s about running a smarter, more efficient business. I’ve seen firsthand how companies that embrace modern scheduling tools outperform their competitors by a mile.
If you’re still relying on outdated field service planning methods, now is the time to change. Trust me, investing in field service scheduling technology will not only save you time and money but also improve your customer relationships and long-term success.
So, what’s the next step for you? What’s one thing you can do today to improve your field service scheduling process?