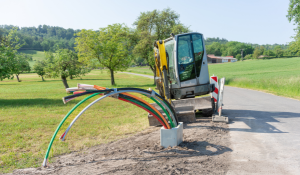
I spend a lot of time talking to field service leaders — operations managers, fleet supervisors, and executives who are constantly looking for ways to do more with less. One thing that always comes up in these conversations is resource wastage. Whether it’s wasted technician time, unnecessary fuel consumption, idle equipment, or redundant manual processes, the costs add up quickly. And in today’s economic environment, nobody can afford that.
That’s where automation makes a real difference. At Field Squared, we’ve seen how automating field service operations helps organizations minimize resource wastage and run leaner, more efficient teams without sacrificing service quality.
Here’s how that plays out in real-world scenarios.
Smarter Scheduling Eliminates Downtime
I’ve talked with many customers who used to spend hours wrestling with spreadsheets. The result? Double-booked appointments, techs sitting idle between jobs, and rushed work that leads to costly rework. With Field Squared’s automated scheduling, we optimize routes and schedules in seconds. The system factors in location, skillsets, job priority, and traffic data. The outcome? Less downtime, more jobs completed, and happier teams.
Cutting Fuel Waste with Smarter Routing
Oregon Aerial Construction told me that before they implemented Field Squared, they had no real oversight into whether field crews were choosing efficient routes. After adopting our route optimization, they quickly saw reductions in fuel costs and mileage. Scale that across hundreds of monthly jobs, and the savings — both financial and environmental — are substantial.
Removing Paperwork Bottlenecks
Paper-based processes slow everyone down and leave room for errors. Lost forms, data entry mistakes, and delayed reporting are all unnecessary drains on resources. Our mobile app allows field teams to capture photos, barcodes, signatures, and notes instantly. Everything syncs with the back office in real time, speeding up invoicing and reporting while eliminating redundant tasks.
Preventative Maintenance That Actually Happens
I’ve met companies that relied on manual logs for preventative maintenance, leading to missed service windows and expensive breakdowns. With Field Squared, maintenance schedules are automated and tracked. No more guesswork — just reliable equipment and fewer unexpected expenses.
Managing Inventory Without the Guesswork
Wasted resources don’t stop at time and fuel. Parts and materials matter, too. Our customers rely on Field Squared to track inventory levels in real time and automate restocking. That means no more overstocking, shortages, or lost assets.
The Takeaway...
Automation isn’t a trend; it’s how smart businesses stay competitive and cut waste. At Field Squared, we help teams work smarter, reduce costs, and deliver better service.
If cutting waste and tightening operations are on your radar, I’d be happy to show you what Field Squared can do. Take a look at our introductory video here.