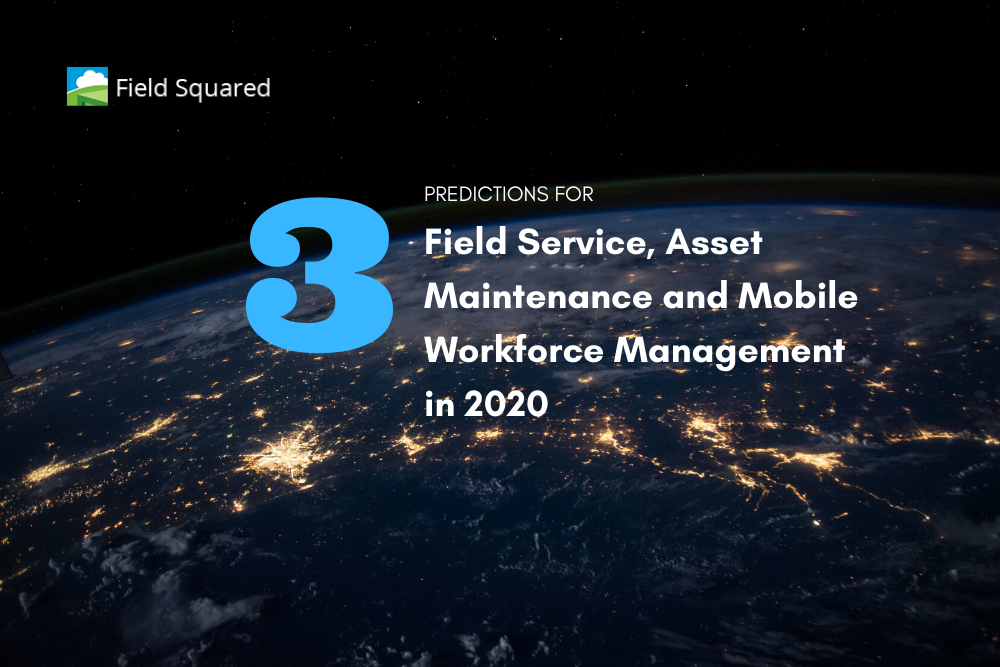
At the end of each year, I reflect on field service industry events and news, and 2019 was no different. I highly recommend this exercise for field operations managers, especially those in executive leadership as way of reinforcing what problems need to be addressed in the coming year.
In my 2019 field service management trends to watch post, a couple predictions I made were spot-on. Across the market, real-time in-app collaboration become increasingly important to field service operations teams. Additionally, partial to complete automation of complex field operations workflows continued to be something many customers specifically came to Field Squared to help implement.
2020 is shaping up to be an even more exciting year. In this post, I will cover 3 field service management, enterprise asset management and mobile workforce management predictions for 2020. Grab a snack and let’s get to it.
#1: All-in-One Field Service Software Gains Momentum
If 2019 was any indication, and here at Field Squared we believe it was, field operations managers were reluctant to adopt disparate tools, systems and software in an effort to increase field efficiency. Time and again over the course of 2019 field service business leaders came to Field Squared seeking a single source of truth; a single solution that had the depth and breadth of capabilities they required.
Moreover, today’s businesses that maintain a highly distributed mobile field workforce do more than field work. The definition has changed, and the lines have blurred. They touch many other aspects of the business, including
- Asset management and maintenance on customer or internally owned assets
- Leveraging GIS (i.e., Esri) across field operations, such as redlining assets
- Managing consumable inventory across warehouses, trucks and work orders
- Quoting and invoicing new jobs while in the field
- Scheduling, and sometimes rescheduling, workers to jobs
- Reporting across field work efficiency or tracking the health of assets with IoT solutions
- Surfacing revenue capture, as well as revenue generating, activities
- Being able to integrate investments the business has already made in third-party and custom, in-house built software/tools/solutions
Differences abound from service business to service business, which compounds the software selection process.
My prediction is 2020 will be the year all-in-one field service automation software increasingly gains momentum. What most businesses are looking for is a consolidated view across their field service, assets and mobile workforce in a single pane of glass. A comprehensive field service automation software opens up an entire new set of opportunities that simply aren’t possible before.
As I mentioned, I saw this in 2019 and even in 2018, but 2020 will see many field service businesses officially designate a project for evaluating, selecting, and implementing a solution.
nbsp;
#2: Artificial Intelligence (AI) Driven Field Service Scheduling Solutions
The past few years artificial intelligence (AI) and, more specifically, machine learning have taken up many journalists’ cycles across the high-tech software space. I predict 2020 to be a turning point for field service businesses to begin exploring what it means to adopt Artificial intelligence (AI) driven scheduling solutions even in instances where it’s not (yet) necessary.
There is an entire category within AI and across what’s known as Operations Research, called constraint satisfaction. According to TechTarget:
“Operations research (OR) is an analytical method of problem-solving and decision-making that is useful in the management of organizations. In operations research, problems are broken down into basic components and then solved in defined steps by mathematical analysis.
The process of operations research can be broadly broken down into the following steps:
- Identifying a problem that needs to be solved.
- Constructing a model around the problem that resembles the real world and variables.
- Using the model to derive solutions to the problem.
- Testing each solution on the model and analyzing its success.
- Implementing the solution to the actual problem.”
Source: TechTarget, Operations Research Definition
Constraint satisfaction is the process of applying AI and Operations Research to find (satisfy) a problem given a set of variables (constraints). I’ve outlined where constraint satisfaction fits into the overall artificial intelligence space.
You may start to see how this type of AI applies to a problem such as scheduling field workers.
Industries differ in terms of both the type of work and the volume of work that takes place on any given day. In reality, it’s still not that simple. Hard and soft constraints affect how scheduling is conducted, including
- Work order intervals daily, weekly, quarterly or even annually
- Inventory needed
- Location related to field worker vs location of work order or asset
- Intraday, dynamic changes in constraints
- Historical information for similar work orders
- Work order types and time to complete by technician
- Asset types and locations
- Unplanned events, such as weather, traffic, road construction, emergency work orders, cancellations, and more
- Vacation and sick time
- Customer service level agreement (SLA) parameter requirements
- Nearest or next available technician
- Special skills, certifications or training parameters
The dynamic nature in the aforementioned complex, nonlinear constraints poses a challenge for the average human to mentally manage simultaneously or even sequentially.
Constraint satisfaction, on the other hand, can be programmed to “think” in such constraints. As constraints enter the scheduling algorithm, small adjustments are made on the data to continually optimize the schedule.
The output is either a human-in-the-loop solution where a proposed schedule is presented to an operations manager who reviews and approves the schedule. Or, a fully automated process that simply schedules the work orders without human intervention.
The former can be utilized across a team of any size or industry and low volatility in schedule changes. The latter is a great option for instances where there is a high volume of work orders to schedule, where volatility in schedules is high and within large teams.
This technology will not go mainstream in 2020, but I foresee an increase in exploration in field service businesses during second half the year.
nbsp;
#3: Video Capture to Enable Remote Asset Management and Maintenance
Along the lines of augmented reality, wearable technology, and virtual reality, having the right tools to more effectively conduct remote asset maintenance is becoming a top priority across many businesses that manage and maintain either internally owned assets or those assets of their customers.
In 2020, video capture will move up the list of requirements for mid- to large size field service businesses. This change will come about because of what I refer to as the field service automation singularity.
Some of you may be familiar with the futurist, Ray Kurzweil. He prophesizes or postulates a coming technology singularity. If not, you can read about it here.
The field service automation singularity is the point at which multiple events occur nearly simultaneously to drive digital transformation. In this case, adopting all-in-one field service automation software that provides the capability to capture video in the field.
The events I speak of include:
- An aging field service workforce with high demand and insufficient supply to replace the outgoing technicians
- Improved mobile device capabilities that native field service mobile apps (i.e., iOS, Android) are able to fully leverage
- Creation of former field technicians turned in-house experts that, instead of being in the field, work at the corporate office or at home and conduct real-time problem-resolution troubleshooting with the field technician
- Reduction of knowledge gaps and building a knowledge library
The field service automation singularity will impact both organizations that focus on field service management and those that focus on enterprise asset management.
Both FSM and EAM can reap the benefits of video capture technology adoption to move their businesses forward in a meaningful way, while further enabling their mobile field workforce with the right tools to more effectively complete work, whatever that may be.
There you have it, 3 Predictions for Field Service, Asset Maintenance and Mobile Workforce Management in 2020. I will continue to follow evolutions in the industry and keep you apprised of my thoughts. I can’t wait to see what 2020 has in store.
Want to learn more about field service automation?
Watch our 90-second explainer video to quickly show you how Field Squared works. View it below.